반응형
[청년 Hy-Po 4기] 강의노트 작성하기 - 반도체 공정 8편
안녕하세요!
SK 하이닉스 청년 Hy-Po 4기 교육생이자 서포터즈 2기로 활동중인 교육생 김세영입니다!
이번편은 미션은 아니지만, 저번 미션 5에서 말씀드렸던 반도체 공정의 강의노트 후속편들을 정리해보려고 합니다!
단순히 핵심만 집중적으로 공략하려고 해요!
그냥 제가 복습하고 공부하면서 작성하는 강의노트라고 생각하시면 될 것 같습니다😁😁
이번편은 반도체 공정의 8번째 편인 "Test & Packaging" 입니다!
그럼 바로 시작해볼까요?
📝 테스트 공정 (Test)
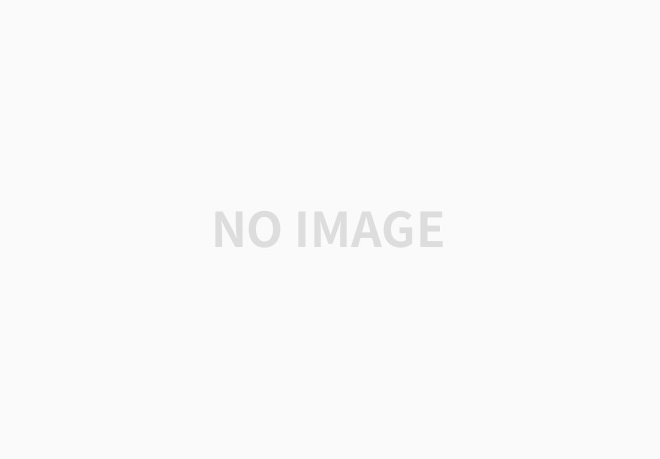
- 전기적 특성 (Electrical Characteristics) 검사를 통해 품질을 테스트 하는 공정
- 초창기 테스트는 양산 제품에 대해 불량 (영구적 오류)를 걸러내는 필터링 위주로 진행
- 현재는 신뢰성 불량을 사전 차단하고, 수율을 향상시켜 원가 절감에 기여하며, 공정의 개선 및 제품의 연구·개발에 도움을 주는 등 그 역할이 점차 확대되고 있음
📝 웨이퍼 테스트 (Wafer Test)
- 테스트 대상이 웨이퍼
- 웨이퍼 위의 수많은 칩들의 특성과 품질을 파악 후 불량 칩이 불필요하게 패키징되는 것을 방지해 원가를 절감
- 반도체 수율과 직결되기 때문에 Repair 가능한 것들은 양품화
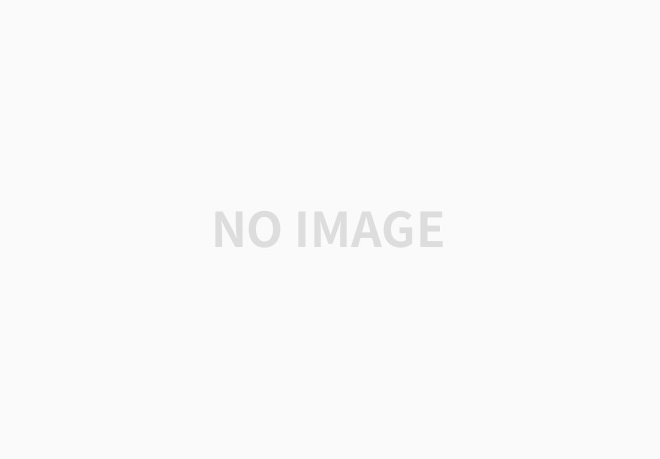
- EPM (ET Test) & WFBI
- EPM (Electrical Parameter Monitoring) IC 동작에 필요한 개별소자들의 전기적 직류 전압, 전류 특성의 파라미터를 테스트해 잘 작동하는지를 판별하는 과정
- WFBI (Wafer Burn-In) 은 웨이퍼에 일정 온도를 가한 다음 AC/DC 전압을 가해 잠재적 불량 요인을 찾아내는 과정
- Pre-Laser (Hot & Cold) Test
- 높은 온도 혹은 낮은 온도에서 전기적 신호를 가해 웨이퍼 상의 각 칩들에 이상이 있는지 판정하고, 불량품 중에서 Repair가 가능한 칩들은 Repair step으로 진행
- Repair & Post Laser (Final Test)
- 불량품에 대해서는 Electrical Rupture를 통해 Repair하고, 수선이 끝나면 Final Test를 통해 수선이 제대로 이루어졌는지 검증하고 양품인지 불량품인지를 최종적으로 판단
- Tape laminate & back grinding
- 해당 공정은 교통카드나 여권에 들어가는 IC 카드를 비롯해 두꼐가 얇은 제품을 조립할 때 필요한 공정
- back grinding은 웨이퍼 후면을 미세한 다이아몬드로 구성된 연마 wheel로 갈아 칩의 두께를 얇게함으로써 조립을 용이하게 해주는 공정
- Tape laminate는 grinding 과정에서 발생하는 Si 잔여물(particle)로부터 웨이퍼 표면 패턴을 보호하기 위해 전면에 UV type을 씌워 보호막을 형성하는 공정
- Linking
- 2, 3번째 단계에서 불량품으로 판정된 침에 특수 잉크를 찍어서 불량품을 식별하도록 하는 과정
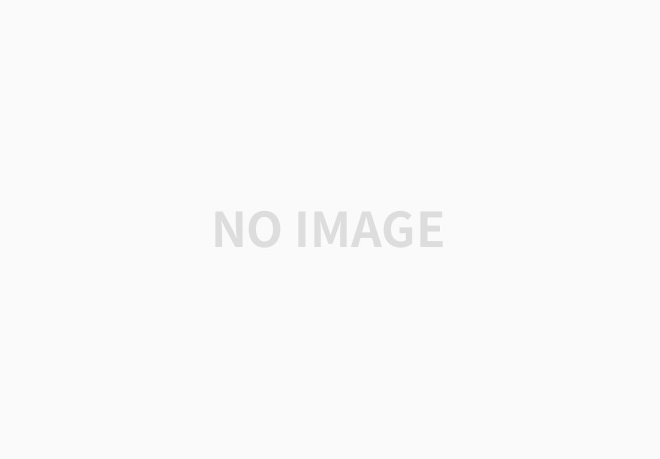
- 매우 가느다란 바늘(탐침)이 웨이퍼가 들어있는 Prob카드에 밀착(Probing)해 전기적인 신호를 인가한 후, 회로를 거쳐 나온 결과인 전기적 특성을 비교·측정해 최종적으로 판정(Die Sorting)함
- 이때, 냉각장치는 테스트 온도 조건에 따라 온도를 인가할 수 있음
📝 패키지 테스트 (Package Test)
- 테스트 대상이 패키지
- 칩을 패키징한 후, 제품을 출하하기 전에 최종적으로 전기적인 특성을 검사하는 단계
- 고객에게 신뢰성 있는 제품을 납품해야 하므로 테스트 공정이 가장 중요
- 양품이 고객에게 전달된 이후에도 칩에 동작오류(Fault)가 발생할 수 있는데, 유저가 일정 기간 칩을 오류 없이 안전하게 사용할 수 있도록 제조 과정에서 약한 칩을 미리 골라내어 신뢰성을 확보하는 것이 중요
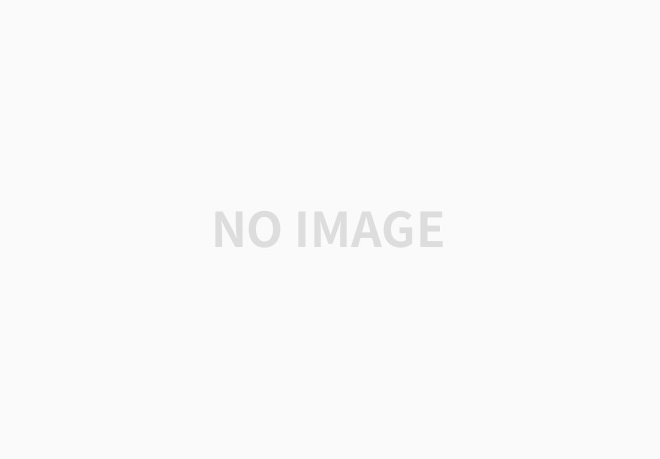
- DC Test & Burn-in
- DC Test를 통해 설계 및 조립공정을 거치면서 발생된 불량을 선별
- Burn-in 공정을 통해 극한 조건을 가한 후 테스트를 진행함으로써 불량 가능성이 있는 제품을 사전에 검사
- Main test
- 데이터시트에 정의된 동작이 사용자 환경에서 정상적으로 동작하는지 판단하는 단계
- 다양한 온도 공간에서 전기적 특성과 기능 검사하고 속도별, 기능별 테스트영역에서 고객이 요구하는 동작이 스펙을 만족하는지 검증
- 반도체 분야 국제표준인 JEDEC Spec을 맞춤
- Visual 검사
- 양품으로 판별된 제품은 납품 전에 마지막으로 패키지 외부에 균열이나 마킹 오류가 있는지 살피는 단계
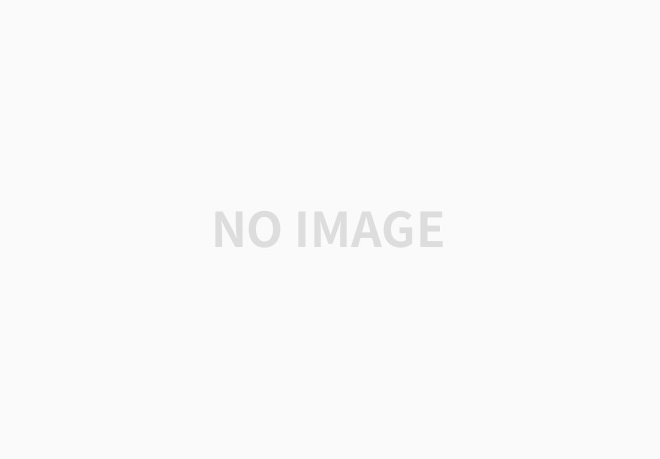
- 패키지 테스트를 위해서 패키지의 핀(pin, 그림에서는 솔더볼)이 아래쪽을 향하도록 패키지 테스트 소켓에 넣어 소켓에 있는 핀들과 물리적으로 접촉
- 그리고 이 패키지 테스트 소켓(포고타입, 러버타입)을 패키지 테스트 보드 (Package Test Board)에 장착하여 패키지 테스트를 진행
📝 모듈 테스트 (Module Test)
- PCB에 8 ~ 16개의 칩을 탑재한 후 진행한다고 하여 보드 테스트라고 함
- 다양한 어플리케이션에서 제품이 CPU의 제어에 따라 여러 동작을 정상적으로 해내는지 검사
- 제품의 특성에 따라 다른 방식으로 진행
- 되도록 고객이 실제 제품을 사용하는 환경에서 칩을 선별
- 불량 칩이 발견되면 양품 칩으로 교환해 새롭게 모듈을 구성

- ET test
- 모듈화 된 제품에 불량 판별을 하기 위해서 ET Test을 통해 선별하는 단계
- Application Test
- 고객이 실제 제품을 사용하는 환경에서 칩을 선별할 수 있도록 하기 위해서 실제 장비에 동작 테스트하는 단계
📝 패키지 공정 (Package)

- 일반적으로 반도체 패키지는 웨이퍼에서 칩을 잘라내고, 칩을 단품화하는 공정
- 0차 레벨 패키지 ~ 3차 레벨 패키지
- 0차 레벨 패키지
- 웨이퍼에서 칩을 자름
- 1차 레벨 패키지
- 칩을 단품화
- 2차 레벨 패키지
- 단품을 모듈 또는 카드에 실장
- 3차 레벨 패키지
- 카드를 시스템 보드에 장착
- 더 이상의 scaling down이 어려움 BUT AI 산업의 발전으로 더 high performance 반도체가 요구되면서
패키징 공정의 중요성이 대두됨
📝 패키지 공정의 목적
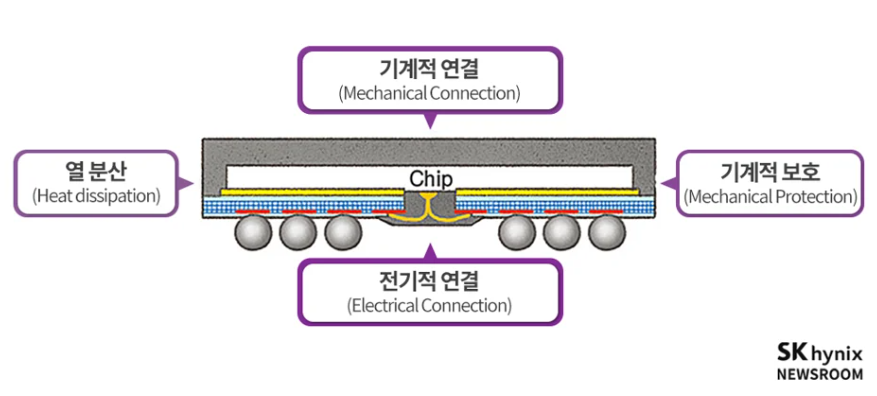
- 열 방출 (Heat Dissipation)
- 소자의 정지를 방지하기 위해 열을 빠르게 발산
- 기계적 보호 (Protection)
- 외부의 기계적 및 화학적 충격으로부터 소자를 보호
- 전기적 연결 (Electrical Connection)
- 전원을 공급하고 신호를 입력하거나 출력을 할 수 있는 통로 생성
- 기계적 연결 (Mechanical Connection)
- 칩이 사용되는 동안 시스템에 잘 부착되어 있도록 연결
📝 패키지 공정 과정

- 라미네이션 (Lamination) 공정
- 회로가 새겨진 웨이퍼 위에 테이프를 붙이는 작업
- 이때, 이 테이프는 패키징 공정 과정에서 웨이퍼의 물리적, 화학적 손상을 막는 보호막 역할
- 백그라인드 (Back Grind) 공정
- 웨이퍼 뒤쪽 표면을 깎아내는 작업
- 웨이퍼를 제품 특성에 맞춰 필요한 만큼 얇게 만들 수 있음
- 최근에 반도체 추세에 맞게 제품 높이를 최대한 낮추는데 기여하는 공정
- 웨이퍼 소우 (Wafer Saw) 공정
- 웨이퍼를 낱개의 다이로 잘라 나누는 작업
- 다이 어태치 (Die Attach) 공정
- 낱개의 다이를 기판 위에 부착하는 작업
- 얼마나 많은 칩을 어떻게 적층하는지에 따라 제품 용량, 기능, 패키지 구조가 결정됨
- 본딩 (Bonding) 공정
- 반도체 칩이 외부와의 전기적 신호를 주고받을 수 있는 구조를 만든다
- 칩과 기판을 가느다란 급속선으로 연결하는 작업인 와이어 본딩(wire bonding) 공정
- 칩 바닥에 범프(bump)를 부착한 후 고온의 열로 기판의 전극에 접합(soldering)해 전기적으로 연결하는 작업인 플립칩 본딩(flip chip bonding)
- 몰드 (Mold) 공정
- 칩과 기판을 외부 충격으로부터 보호하기 위해 외곽을 감싸는 작업
- 칩과 기판을 금형에 넣고 에폭시 수지를 이용해 외곽을 감싸는 방식
- 마킹 (Marking) 공정
- 표면 위에 반도체 종류, 제조가 등 제품에 대한 정보와 고객이 원하는 특정 표식을 새기는 작업
- 솔더블 마운트 (Solder Ball Mount) 공정
- 기판 뒷면에 솔더볼을 안착한 뒤 가열시켜 접합하는 작업
- 반도체를 전자기기 내부의 인쇄회로기판(PCB)에 연결하는 역할을 수행
- 싱귤레이션 (Singulation) 공정
- 반도체 기판이 낱개의 칩으로 분리되면 비로소 하나의 반도체 제품 완성
이렇게 해서 반도체 공정과 관련된 핵심 개념 정리가 끝났습니다!!
다시 둘러보니 회로 이론 부터 반도체 물성 및 소자를 거쳐 공정까지 대부분의 내용을 정리해보았습니다!
청년 하이포 활동을 하면서 복습하는 느낌으로 작성했는데 끝날 시기에 돌아보니 너무 뿌듯합니다😎😎😎
하이포 활동과 관련된 피드는 아마도 여기서 끝나겠지만!
그래도 제 블로그에 글을 작성해서 올리는 건 시간이 남는대로 꾸준히 해볼 예정입니다!
기대해주세요!😊😊😊
LIST
'대외활동 > SK하이닉스 청년 Hy-Po 4기' 카테고리의 다른 글
[찐_최_최_최_최종 후기] SK 하이닉스 청년 Hy-Po 4기 최종 후기 (9) | 2024.03.08 |
---|---|
[청년 Hy-Po 4기] 강의노트 작성하기 (반도체 공정 7편) (0) | 2024.02.25 |
[청년 Hy-Po 4기] 강의노트 작성하기 (반도체 공정 6편) (0) | 2024.02.25 |
[청년 Hy-Po 4기] 강의노트 작성하기 (반도체 공정 5편) (0) | 2024.02.25 |
[청년 Hy-Po 4기] 강의노트 작성하기 (반도체 공정 4편) (0) | 2024.02.25 |